What is the cost of production? This is an important factor that directly affects revenue and profit of each business. Understand production costs and how to effectively manage business finances will help businesses optimize product costs, improve competitiveness and achieve sustainable growth goals.
In this article, let's Bizzi learn more about What is the cost of production?, Classification of production costs, calculation methods as well as important notes to help businesses control costs well and optimize profits.
What is the definition of cost of production?
Total costs (including costs directly attributable to the product or indirectly allocated) that a business must pay to produce a product or service. This is an important factor in determining the cost and profit of the business.
- Production costs include: Labor, raw materials, production supplies, management and operating costs.
- Production and business costs: The cost of live labor and materialized labor that a business spends in relation to production and business activities in a certain period. Production costs can be high/low depending on the level of activity.
- For example:
- Businesses that produce confectionery, clothing, and furniture need costs for raw materials, rent, and employees.
- Service industry (restaurants, beverage shops, shopping malls) need costs for labor, raw materials, and depreciation of fixed assets.
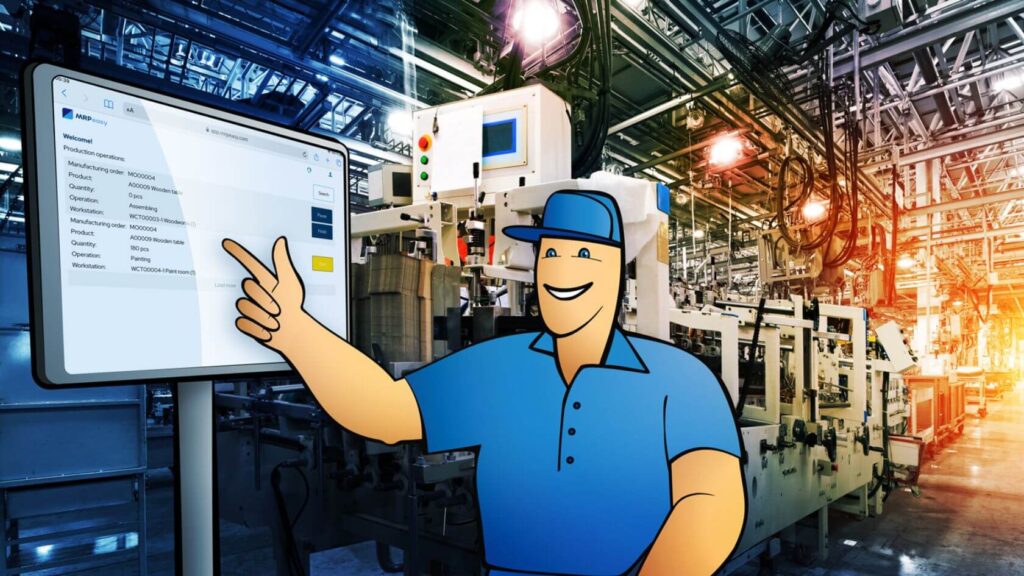
Characteristics of production costs
- Production costs increase as order quantity increases and vice versa.
- Continuously arising during the production process.
- Depends on many factors: Impact by production technology (using modern technology to reduce costs), raw material prices, labor market.
- Complex structure, including fixed cost and variable cost.
- Need to optimize to increase profits.
- Decide on product selling price.
What is the role of production costs in business?
- For business:
- Reflecting the production status
- Help managers have an overview, thereby building measures to improve quality and save costs.
- For management:
- Avoid waste and increase profits
- Impact on inventory management
- Provide information for managers to make business production management decisions.
- For the market:
- Products with reasonable prices attract customers and increase market share.
- Shape business strategy and develop financial plan
- For the state:
- State economic agencies can have a comprehensive and objective view of the development of the country's economy, thereby proposing correct policies and guidelines to promote economic development.
Distinguish between production costs and business costs
Criteria | Production Cost | Business Costs |
Nature | The cost of creating a product/service. | Cost of selling & operating a business. |
For example | Raw materials, labor, electricity and water production. | Advertising, sales staff salaries, shipping costs to customers. |
Affect | Directly affects product price. | Impact on business profits. |
Classification of production costs
By economic nature
- Direct material cost: Costs directly related to production and specifically determined for each product (main raw materials, auxiliary materials, packaging).
- Direct labor costs: Costs directly related to production and specifically determined for each product (salary, allowances, insurance).
- General manufacturing costs: Costs related to production but cannot be specifically identified for each product (fixed asset depreciation, maintenance, repair, indirect materials, indirect labor, outsourced services).
- Cost factor:
- Raw material factor.
- Fuel and power factor.
- Salary and salary allowances factors.
- Social insurance, health insurance, and unemployment insurance factors.
- Fixed asset depreciation factor.
- Outsourcing service cost factor.
- Other cost factors in cash.
By purpose and use
- Cost of raw materials: Cost of main materials, accessories, packaging,...
- Labor costs: Salary, allowance, insurance,...
- General manufacturing costs: Fixed asset depreciation costs, maintenance, repair, indirect materials, indirect labor, outsourced services, etc.
- Outsourcing service costs: Transportation, insurance, agent commission, brokerage,...
- Cost of production tools: Purchase, maintenance, repair of production equipment,...
- Other costs: Research and development, production management,…
According to the relationship with the volume of work, products in the period
- The variable costs: Changes in quantity are directly proportional to changes in production volume (raw material costs, direct materials, direct labor costs).
- Fixed costs: No change in total when there is a change in the volume of products produced within a certain level (fixed asset depreciation cost).
According to the production and manufacturing technology process
- Raw material production cost: Arising from the use of raw materials in the production process.
- Labor costs: Arising from the use of labor in the production process.
- General manufacturing costs: Arising during production But it is not possible to determine specifically for each type of raw material cost and labor cost.
- Basic cost: Direct and fixed costs in each specific step of the production or manufacturing process.
- General manufacturing costs: Costs that cannot be specifically allocated to each stage in the production process.
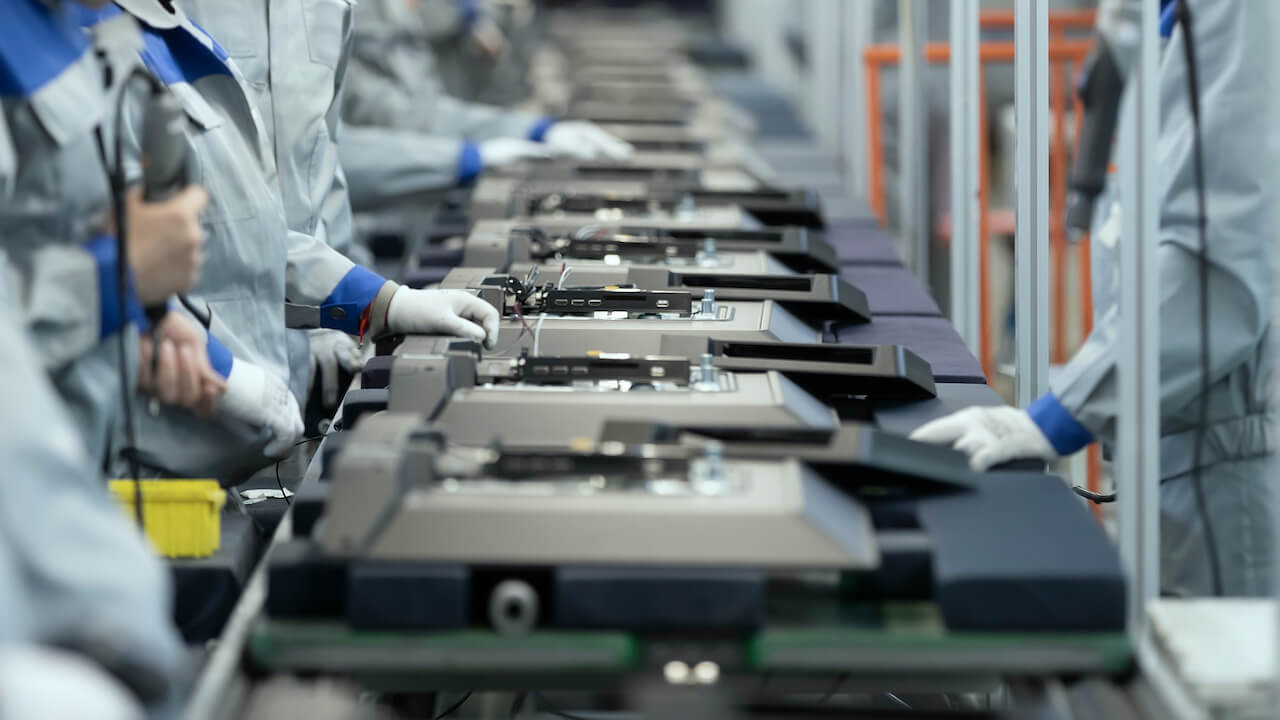
According to the method of concentrating production costs on cost-bearing objects
- Direct costs: Production costs are directly related to the production of a certain product or service.
- Indirect costs: Costs associated with many types of products and services.
According to cost composition
- Single cost: Costs made up of a single cost element (main raw material costs, wages, fixed asset depreciation costs).
- Total cost: Cost includes many different elements but has the same function (overall production cost).
What is the formula for calculating manufacturing costs?
- Basic formula: Production cost = Raw material cost + Production labor cost + Machinery and equipment cost + Production management cost + Other costs.
- Cost of raw materials: Quantity of raw materials required x Unit value of raw materials.
- Production labor costs: Number of hours of labor required x Average wage of production workers.
- Cost of machinery and equipment: Value of machinery and equipment / Average life of machinery and equipment.
- Production management costs: Salaries and benefits of production management staff + Production facility operating costs.
- Other costs: Transportation, insurance, rental and other support costs.
Examples of manufacturing costs in business
- Woodworking factory:
- Material costs: Wood, glue, paint.
- Labor costs: Carpenter and painter salaries.
- Machinery and equipment costs: Saws, sanders, coating machines.
- Production management costs: Factory management staff salaries, factory operating costs.
- Other costs: Transportation of raw materials and products, marketing, factory maintenance.
- Vinamilk Company:
- Raw material costs: Fresh milk, milk powder, sugar, flavoring, milk cartons and packaging.
- Labor costs: Salaries and benefits for production employees.
- Machinery and equipment costs: Maintenance and repair costs.
- Service industry: *Labor costs, equipment costs, general production costs.
How to optimize production costs for businesses
Optimize production costs help businesses reduce product costs, increase profits and improve competitiveness. Below are effective solutions to help businesses reduce production costs 10 - 30%, improve profits while still ensuring product quality.
Optimize raw material production costs:
- Negotiate with suppliers for better prices.
- Find different suppliers to compare prices.
- Periodically evaluate and change suppliers as needed.
- Use recycled materials or make use of surplus parts.
Optimize production labor:
- Improve labor productivity by training employees to improve skills, avoiding waste of time and materials.
- Applying machinery and technology to production to reduce manual labor.
- Invest in robots and automated production lines to improve efficiency.
Reduce storage costs:
- Calculate and use raw materials reasonably to ensure safe inventory.
- Only import goods when needed to reduce storage costs and avoid excess inventory.
- Apply promotions, discounts, and giveaways to solve inventory problems.
Reduce defective product rate: Good quality control in the production process.
- Establish clear quality control procedures.
- Apply advanced technologies.
Production management software application:
- Helps save labor costs
- Improve performance and efficiency of quality management
- Optimize resources, optimize working shifts, avoid excess or shortage of personnel.
- Recruiting and training highly skilled workers.
- Optimize management costs.
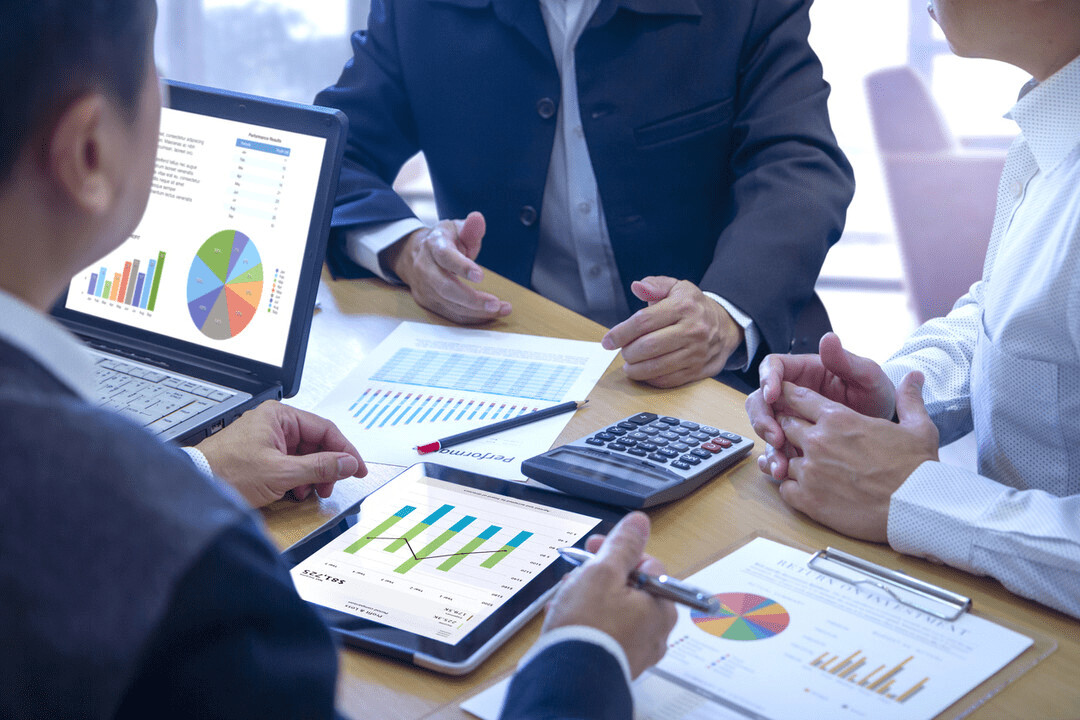
The relationship between production costs and product prices
- Product cost: Costs incurred directly for the production of products in the workshop (direct materials, direct labor, general manufacturing costs). This cost depends on the quality of input materials – Good materials help reduce costs.
- Production cost: Includes production costs and indirect costs contributing to the production process (salaries of company accountants, office supplies, management costs).
- Relationship:
- Production costs are the basis for product cost components
- Product cost is a measure of the production costs that a business spends to get the volume of finished products.
What are the benefits of applying ERP to production cost management?
Application ERP software Incorporating into a business has the following outstanding benefits:
- Cost control, production cost
- Demand planning from orders, raw materials, production plans
- Tight inventory control
- Supply chain management
- Manage and record production progress
- Evaluate the level of cost savings
- Shape business strategy and develop financial plan
How does Bizzi help leaders manage production costs?
Bizzi is built on in-depth analysis and caters to every need. cost management and control your business budget in the simplest way. Here's how expense approval automation Bizzi can help your organization:
Support in developing cost policies for the organization
- Easy to set up expense usage policy
- Manage billing information for each user: MST, invoice receipt email, address, personal information
- Manage expense categories on demand
Standardize the automatic cost creation and approval process
- Build a approval process flow for each spending limit, suitable for the cost nature of each company.
- Decentralize approval and management of permission groups according to each department level
- Create and send spending requests according to various categories: travel, business trips, reception, stationery, etc.
- Create and approve payment requests and expenses conveniently anytime, anywhere, instantly via mobile app
- Conveniently attach information Electronic invoice, vouchers for each cost
Expense management departments and projects in real time
- Record expenses quickly in real time
- Manage costs by each category/department/project
- Minimize risk and reconcile payments faster
- Allow exporting excel file of expense list
Control costs strictly according to budget
- Establish and allocate budgets by fiscal year with organization/project/department size
- Proactively control budgets with the ability to set spending limits and assign budgets to each category/department/project
- Automatically warn when spending exceeds the allocated budget
- Easily track remaining budget information and spent expenses
- Dashboard system reports budget compared to reality to help evaluate performance and effective financial operations
- Synchronize with the organization's cost management system and payment request approval process
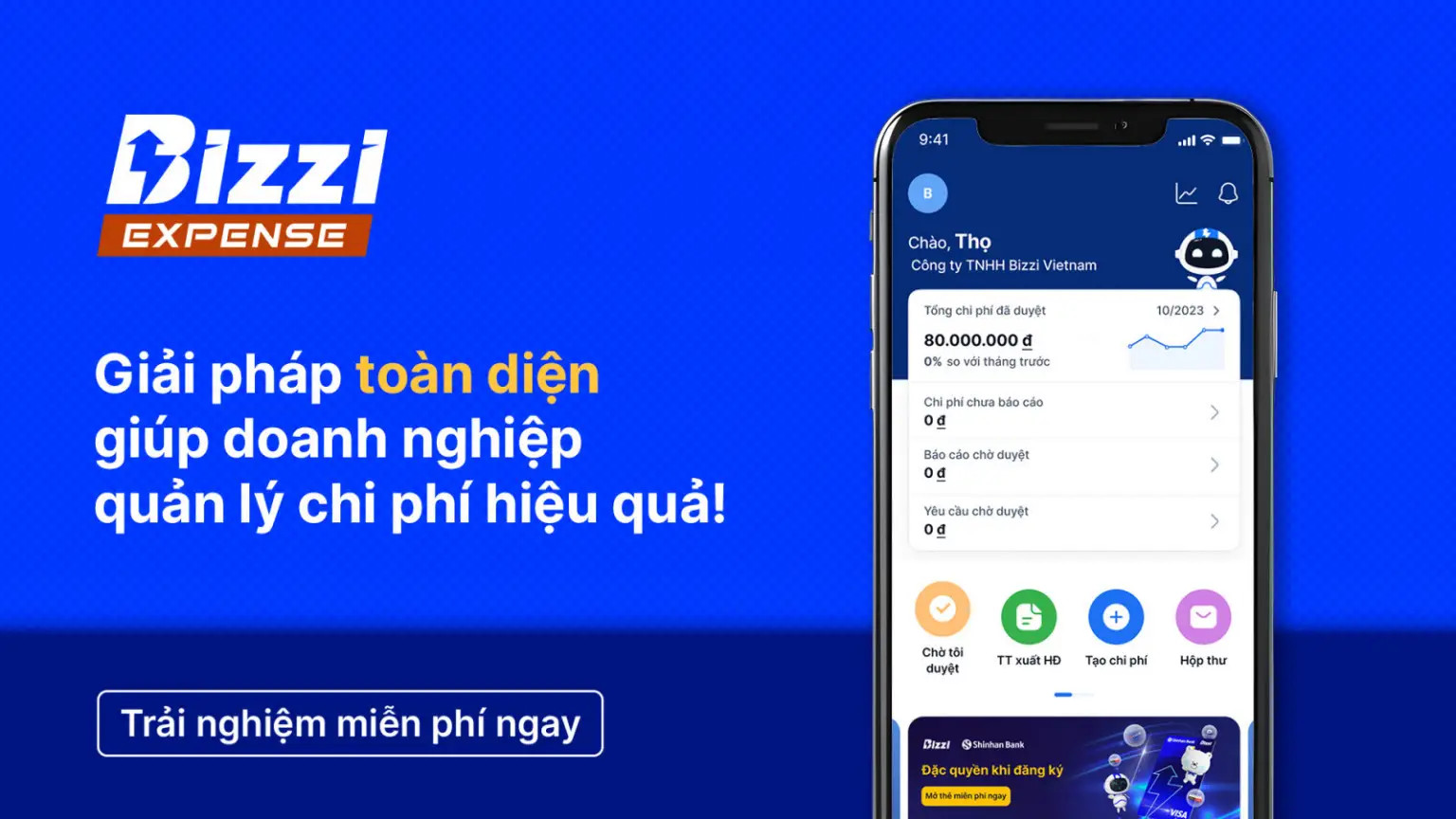
In the context of economic fluctuations and increasingly fierce competition, effective control of production costs becomes a key factor for businesses to maintain profits and ensure sustainable development. By understanding what your production costs are and using Bizzi’s comprehensive cost management platform, you can streamline your processes, gain an overview of your business’s spending habits, and control your cash flow in the most optimal way. This has the potential to help businesses improve efficiency, reduce costs, and increase return on investment (ROI).
Schedule a demo with Bizzi today and discover how our innovative solutions can help you navigate the complexities of manufacturing cost management in particular and business costs in general with ease.
- Link to register for a trial of Bizzi products: https://bizzi.vn/dang-ky-dung-thu/
Read more: