Many people think that MRP is a shortened form of ERP, but in fact MRP is a part of ERP (usually a module in modern ERP). Therefore, if ERP and MRP are not clearly compared, businesses may have wrong expectations or misjudge the system's capabilities.
Follow the article below for a more specific perspective on these two solutions.
Overview of MRP system
First, let's understand the concept of MRP. What is MRP? What problems can MRP solve for businesses?
Definition of MRP
MRP stands for “Material Requirements Planning”. It is a software solution designed to help manufacturers calculate exactly what materials are needed, when, and in what quantities.
The main objective of MRP is to facilitate production control, planning and reporting. This software helps manufacturing businesses plan to prepare and manage the raw materials needed for the production process, avoiding shortages or surpluses of raw materials, thereby minimizing waste and disruption.
Main functions of MRP
The main tasks of the MRP system include:
- Forecast: Analyze production and sales forecasts to determine raw materials, components, and supplies needed for production.
- Inventory management: Ensure adequate raw materials, components and supplies are available in stock, track and manage inventory to maintain optimal levels. The system automatically tracks when reorders are needed and can place orders directly.
- Production scheduling: Analyze and create efficient production schedules, optimizing production orders based on factors such as available raw materials, supply schedules, and expiration dates. This helps minimize waste and maximize material utilization.
- Track orders and inventory: Track raw material and supplies order status, maintain up-to-date schedules. Manage finished and semi-finished products, as well as delivery processes.
Evolution of MRP to MRP II
Over time, MRP has evolved to include more features. Most current MRP systems (often referred to as MRP II – Manufacturing Resource Planning) have incorporated different modules. MRP II provides more advanced features such as detailed capacity planning, schedule management, shop floor control, financial accounting, equipment management, labor allocation, quality management, and manufacturing cost control. MRP II is the premise for the development of enterprise resource planning (ERP) systems.
Which businesses need MRP?
- Manufacturing enterprises: especially assembly production, with many raw materials and stages.
- Companies with complex BOMs: such as electronics, machinery, textiles, packaged foods…
- Businesses need to plan production and purchases accurately.
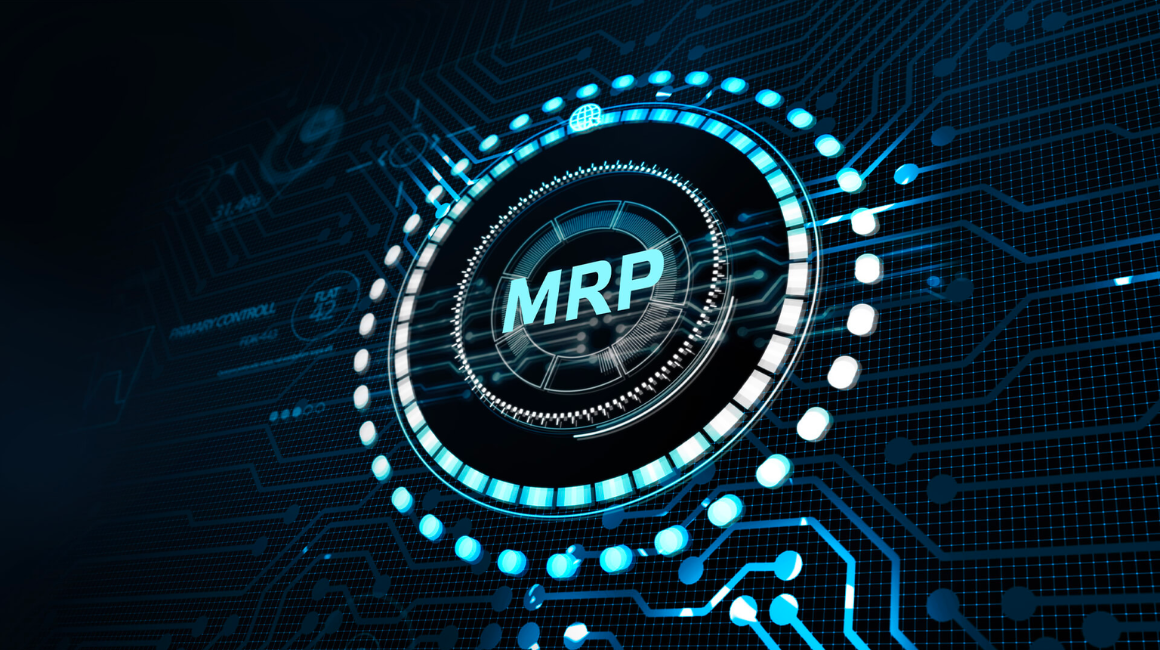
Overview of ERP system
Below is complete and easy-to-understand information about the ERP (Enterprise Resource Planning) system, which is essential for modern businesses, especially in today's fiercely competitive environment.
What is ERP?
ERP stands for Enterprise Resource Planning. It is a more comprehensive and complete software system than MRP. ERP helps manufacturers automate and streamline business processes, not just related to production but across their entire business. ERP is designed to connect and integrate every aspect of the business into a single database, helping to streamline tasks and processes, and share information effectively across the entire organization. This results in accurate data, which helps increase efficiency and reduce costs across every aspect of the business.
Main modules and functions of ERP
Comparing ERP and MRP, it can be seen that ERP is not limited to the manufacturing sector like MRP, but also brings comprehensive benefits to every aspect of the business organization. The most popular ERP modules include:
- Finance – Accounting: Helps businesses track accounting, prepare financial reports, automate income and expense management, manage payables and receivables, budget, forecast, asset management and compliance.
- Human Resource Management (HR): Enables businesses to track attendance, calculate payroll, manage employee data, benefits, recruiting and performance management.
- Sell: Track leads, customer conversations, goals, and sales performance. This module automates sales processes and generates data-driven analytics.
- Supply chain and logistics management: Material and inventory balancing, including inventory management, logistics, warehouse management and order fulfillment.
- Manufacture: Simplify multi-step manufacturing processes, including production planning, material requirements planning (MRP), and quality management.
- Project Management: Support planning, scheduling, executing and monitoring projects, managing resources and tracking costs.
- Other common modules may include research and development (R&D), engineering, asset management, sourcing and procurement.
ERP implementation method
ERP systems can be deployment in a variety of ways, including on-premise software or cloud-based software (Cloud ERP). Businesses can choose to purchase the software or rent it on a monthly basis.
Which of the above companies implement MRP?
- Manufacturing, retail, trade, distribution, service businesses
- Enterprises with 20 or more employees
- Businesses have difficulty in data management, fragmented processes, and lack of connectivity.
- Businesses want to expand, control finances and operate tightly.
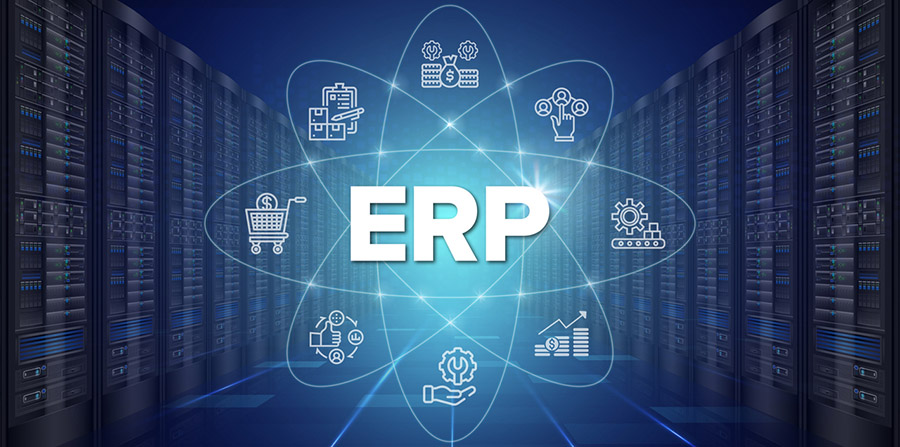
What is the relationship between ERP and MRP?
ERP and MRP work together to optimize business operations. MRP software functions as a subsystem or function within the manufacturing management subsystem of an ERP solution. MRP provides information about materials and resources to the ERP solution, which integrates and uses that data to inform other business units.
For example, the finance department would use the information that the MRP solution provides to ERP to calculate accounts receivable and manufacturing costs to determine product pricing.
Both technologies have dramatically shaped the manufacturing industry, increasing efficiency and productivity while reducing production time. Comparing ERP and MRP will help managers better understand the advantages of each solution and take advantage of the best for their business.
Comparing ERP and MRP
Below is a comparison of ERP and MRP – two popular management tools but with different goals and scopes. Depending on the size, industry and operational needs, businesses will have the appropriate choice.
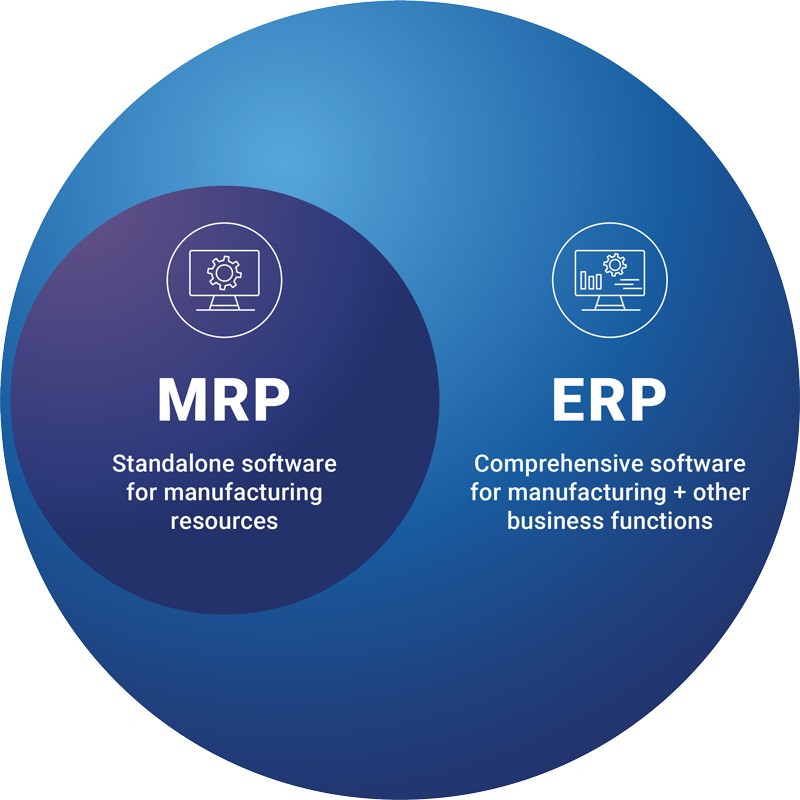
Scope and objectives of management
The main difference when comparing ERP and MRP is that ERP systems help plan and automate many business functions across an enterprise. The primary goal of ERP is to facilitate financial management and reporting, which is directly related to accounting, manufacturing, supply chain, customer management, quality, processes, and planning.
In contrast, MRP systems focus on materials management and production planning. The central objective of MRP is to facilitate production control, planning, and reporting, with a narrower scope for ordering and planning materials.
Integration capabilities
ERP is a comprehensive business management software that automates and integrates all the different software on a single platform, easily integrated with other solutions. This helps to streamline tasks and processes, and share information effectively across the entire organization.
In contrast, MRP is more of a standalone system. While some MRP systems can be combined with other systems or integrated with third-party applications (including ERP), this can be challenging or is not the primary focus of MRP. MRP does not include financial management or CRM software features.
User Object
Due to its broader scope, people from different departments within a business can use ERP software. ERP is suitable for businesses across all industries, including manufacturing, distribution, retail, services, finance, etc.
Meanwhile, those who are involved in manufacturing operations can use MRP tools. MRP is mainly used by manufacturing companies that need to manage production resources. Comparing ERP and MRP will help businesses choose which tool for their business.
Investment costs
As a simpler and narrower solution, MRP systems are often less expensive. ERP is a comprehensive business management system that can perform many different functions in one system, so this solution is often more expensive to implement, train, and maintain. However, cloud-based solutions (Cloud ERP) can offer a relatively more affordable price, suitable for both small and medium-sized businesses.
Ability to meet business growth
A company that is looking to grow significantly will need to rely more on automation and standardized, streamlined processes to succeed and keep up with growth. This requires an ERP system that is scalable to accommodate additional tasks in the future. If your company is expected to maintain consistency or is focused solely on manufacturing, you may only need an MRP tool.
Choosing the right software for your business
There is no “best” software for every business, but rather which software best suits your specific needs. Compare ERP and MRP so that businesses can find answers to the following questions to know which software is right for them. Choosing an ERP or MRP system depends on a number of important factors below:
Identify goals and needs
- If you just need to improve your manufacturing processes and inventory control, an MRP system may be all you need. MRP is specifically designed to serve this purpose and is more cost-effective.
- If you want to optimize, automate and connect processes not only from manufacturing but also to accounting, HR, sales, etc., you will need ERP software. ERP will fully meet the integration requirements of the business.
Consider the budget
- The costs associated with licensing, implementing, training, and maintaining an ERP system are often quite high due to its size and complexity. However, the business optimization that ERP brings can lead to efficiency and increased productivity rates, which can pay for itself in the long run. Businesses need to accurately analyze the Total Cost of Ownership (TCO) and Return on Investment (ROI).
Development orientation assessment
- If your company is growing rapidly and is geared towards scaling operations, requiring more automation and standardized processes, an ERP system is necessary.
- If your business expects to maintain consistency or long-term sustainable growth, and remains focused solely on manufacturing, you may only need an MRP tool.
Bizzi – Specialized solution to support corporate financial management
Bizzi is an invoice processing and financial management automation platform, designed to optimize accounting and financial processes, especially suitable for integration with ERP systems of medium and large enterprises. Bizzi does not replace ERP, but complements, accelerates, and optimizes the efficiency of financial operations, especially accounts payable (AP).
Why do businesses need Bizzi besides ERP?
ERP systems are very powerful in synthesizing operational data, but there are still some limitations in financial and invoice processing such as:
Limitations of ERP | Bizzi solved it by |
Manual invoice processing, prone to errors | Automatically read and extract invoice data using OCR + AI |
Lack of warning of incorrect invoices, risky invoices | Integrate real and fake invoice lookup from General Department of Taxation |
Slow payment processing due to cumbersome approval process | Automatic rotation – approve invoices according to flexible workflow |
Difficult to control supplier debt | Invoice lifecycle management & real-time debt reconciliation |
Time consuming data entry into ERP | Automatically synchronize data to ERP, no manual operation required |
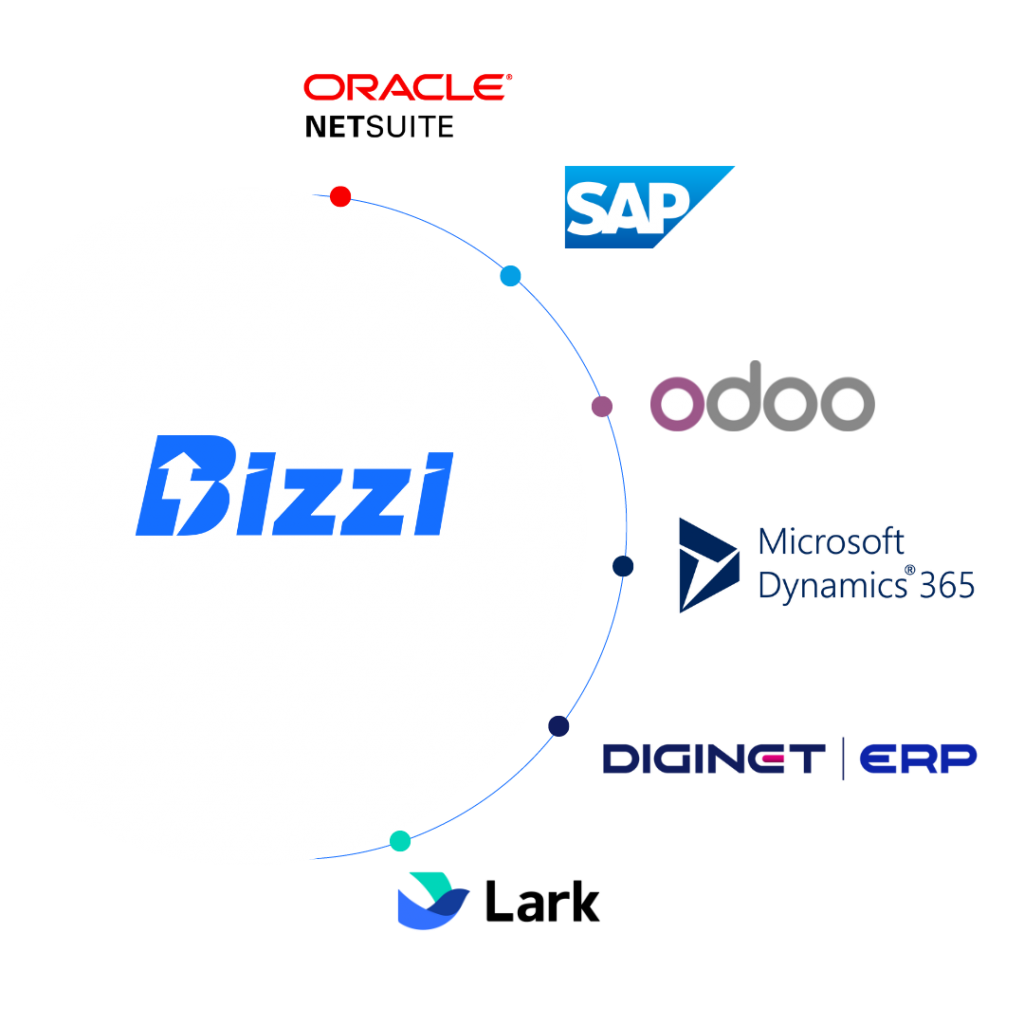
Bizzi automates invoice processing and expense management:
- Processing input invoices: Automate invoice uploading, verification, and reconciliation using robotic process automation (RPA) and artificial intelligence (AI). The system can automatically compare invoice details with purchase orders (POs) and warehouse receipts (GRs) in real time to detect discrepancies. It also has the ability to verify valid suppliers, automatically record and electronic invoice storage with long-term retention period (e.g. 10 years), and risk invoice warning.
- Business expense management: Helps digitize the entire process of creating payment requests and approving business expenses, ensuring transparency and efficiency. The solution allows setting up budgets by department/project, monitoring expenses against the allocated budget, and warnings when exceeding the budget. The system supports an automatic and flexible expense approval process, real-time expense tracking, and generating detailed expense reports.
- Business expense management: Enables automatic flight booking integrated with ticketing services, manages all business expenses such as airfare, hotel, transportation, food. Can set spending limits for each employee or business trip, require pre-approval for business trips and provide comprehensive business expense reports.
Bizzi helps businesses manage debt and finance:
These solutions provide tools to track and control receivables. They may include:
- Automatic debt reminder: Create a debt reminder process based on a script via email or text message.
- Track and reconcile debt: Automatically record and track debts of each customer and supplier, warn of due or overdue debts, and reconcile debts. The system can also generate detailed reports on debt status.
- Connecting capital sources: Some platforms also facilitate businesses' access to capital through supply chain finance or working capital financing options, supporting small loans with quick disbursement times.
Bizzi has the ability to integrate with business management systems:
Bizzi has integration capabilities Seamlessly integrate with existing business management systems, including enterprise resource planning (ERP) systems and accounting software. Flexible API integration enables cost and budget data to be synchronized from multiple sources into a single platform, enhancing the functionality of existing infrastructure without completely replacing it.
This allows businesses to leverage expertise in financial automation while maintaining broader financial control from the overall management system.
Conclude
Comparing ERP and MRP, it can be seen that both are useful management tools, especially in manufacturing, and each has its own advantages and disadvantages. Small businesses that focus on production and inventory can benefit greatly from a dedicated MRP system. Meanwhile, large businesses with broader management needs, diverse operations, and a desire to integrate all business processes will be better suited to an ERP system.
Additionally, dedicated financial automation solutions like Bizzi can be an attractive option for businesses looking to streamline specific financial back-office processes, especially when they can integrate with existing business management systems. Choosing the most appropriate software will depend on the size, current needs, implementation goals, budget, and growth direction of each business.
To get advice and try Bizzi's solutions, click to register here: https://bizzi.vn/dat-lich-demo/